Flange Facing Machine: Essential Tool for Precision Flange Resurfacing
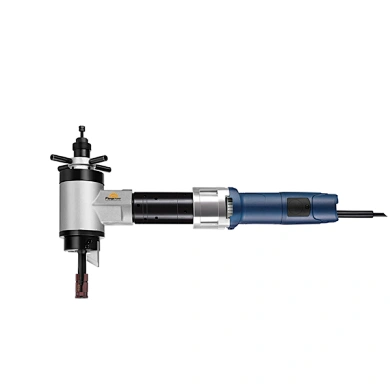
。
# Flange Facing Machine: Essential Tool for Precision Flange Resurfacing
## What Is a Flange Facing Machine?
A flange facing machine is a specialized tool designed to resurface and repair damaged or corroded flanges. These machines are commonly used in industries such as oil and gas, petrochemical, power generation, and shipbuilding where flange connections play a critical role in piping systems.
## Why Flange Resurfacing Matters
Properly machined flange faces are essential for creating leak-proof connections in piping systems. Over time, flanges can become damaged due to:
– Corrosion
– Gasket imprinting
– Mechanical damage
– Improper installation
– Normal wear and tear
A flange facing machine allows technicians to restore these damaged surfaces to their original specifications without requiring complete flange replacement.
## Types of Flange Facing Machines
There are several types of flange facing machines available:
### Portable Flange Facers
These lightweight, compact machines can be easily transported to job sites and mounted directly onto the flange. They’re ideal for field repairs and maintenance work.
### Stationary Flange Facing Machines
Larger, more powerful machines designed for shop use where flanges can be brought to the machine for resurfacing.
### CNC Flange Facing Machines
Computer-controlled machines that offer the highest level of precision and repeatability for critical applications.
## Key Features to Consider
Keyword: Flange facing machine
When selecting a flange facing machine, consider these important features:
– Cutting capacity (diameter range)
– Power source (electric, hydraulic, pneumatic)
– Mounting system
– Cutting tool options
– Portability
– Accuracy and repeatability
– Ease of operation
## The Flange Facing Process
The typical flange facing process involves these steps:
1. Inspection and measurement of the existing flange
2. Proper mounting and alignment of the facing machine
3. Selection of appropriate cutting tools
4. Machining the flange face to required specifications
5. Final inspection and surface finish verification
## Benefits of Using a Flange Facing Machine
Investing in quality flange facing equipment offers numerous advantages:
– Cost savings by extending flange service life
– Reduced downtime for repairs
– Improved safety by ensuring proper sealing surfaces
– Versatility for various flange types and sizes
– Compliance with industry standards and specifications
## Maintenance Tips for Flange Facing Machines
To ensure optimal performance and longevity:
– Regularly clean and lubricate moving parts
– Inspect cutting tools for wear
– Check alignment and calibration periodically
– Store properly when not in use
– Follow manufacturer’s maintenance schedule
## Choosing the Right Machine for Your Needs
Selecting the appropriate flange facing machine depends on several factors:
– Frequency of use
– Range of flange sizes to be serviced
– Available workspace
– Budget constraints
– Required precision levels
For most industrial applications, a portable flange facing machine with a wide diameter range offers the best combination of versatility and practicality.
## Conclusion
A flange facing machine is an indispensable tool for maintaining and repairing critical flange connections in industrial piping systems. By restoring damaged flange surfaces to their original specifications, these machines help prevent leaks, ensure system integrity, and extend the service life of valuable piping components. Whether you choose a portable unit for field work or a stationary machine for shop use, investing in quality flange facing equipment will pay dividends in improved reliability and reduced maintenance costs.
Leave A Comment