Flange Facing Machine: Essential Equipment for Precision Machining
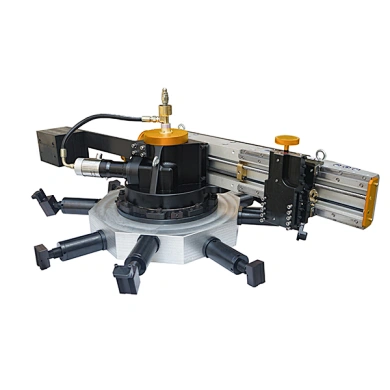
# Flange Facing Machine: Essential Equipment for Precision Machining
## Introduction to Flange Facing Machines
Flange facing machines are specialized tools designed for machining and resurfacing flanges in various industrial applications. These machines play a crucial role in maintaining the integrity and functionality of piping systems, pressure vessels, and other critical equipment where flanges are used.
## Key Features of Modern Flange Facing Machines
Modern flange facing machines come equipped with several advanced features that enhance their performance and versatility:
– High-precision cutting capabilities
– Adjustable cutting speeds
– Portable designs for on-site machining
– Compatibility with various flange sizes
– Automated feed mechanisms
– Digital measurement systems
## Applications in Industrial Settings
Flange facing machines find extensive use across multiple industries:
### Oil and Gas Industry
In the oil and gas sector, these machines are essential for maintaining pipeline connections and ensuring proper sealing of flange joints under high-pressure conditions.
### Power Generation
Power plants utilize flange facing machines to maintain turbine connections and other critical flange joints in steam and gas systems.
### Chemical Processing
Chemical plants rely on these machines to ensure leak-proof connections in their piping systems, where even minor imperfections can lead to hazardous situations.
## Benefits of Using Flange Facing Machines
The advantages of incorporating flange facing machines into maintenance operations are numerous:
– Cost-effective alternative to flange replacement
– Reduced downtime for equipment maintenance
– Improved safety by ensuring proper flange sealing
– Extended service life of existing flanges
– Precision machining capabilities for optimal surface finish
– On-site operation eliminates the need for component removal
## Choosing the Right Flange Facing Machine
When selecting a flange facing machine, consider these important factors:
– Maximum flange diameter capacity
– Power requirements
– Portability needs
– Cutting tool compatibility
– Accuracy specifications
– Ease of setup and operation
– Available accessories and attachments
## Maintenance and Care Tips
Proper maintenance ensures optimal performance and longevity of your flange facing machine:
– Regularly clean and lubricate moving parts
– Inspect cutting tools for wear and replace as needed
– Store the machine in a dry, clean environment
– Follow manufacturer’s guidelines for routine maintenance
– Calibrate measurement systems periodically
– Train operators on proper usage techniques
## Future Trends in Flange Facing Technology
The flange facing machine industry continues to evolve with technological advancements:
– Integration of IoT for remote monitoring
– Development of more compact and lightweight designs
– Improved automation features
– Enhanced cutting tool materials for longer life
Keyword: Flange facing machine
– Advanced digital measurement systems
– Energy-efficient motor technologies
Flange facing machines remain indispensable tools for precision machining in industrial maintenance operations. Their ability to restore flange surfaces to optimal conditions while saving time and resources makes them valuable assets across various sectors. As technology advances, these machines will continue to offer improved performance, accuracy, and efficiency for industrial applications.
Leave A Comment